Maintaining a well-groomed lawn is a rewarding task, but it can become frustrating when your lawn mower encounters hardware errors. One common issue faced by mower owners is “Hardware Error 3.” This error can halt the mowing process and leave you scratching your head for a solution. In this comprehensive guide, we will delve into the causes behind hardware error 3 and provide you with detailed step-by-step instructions on how to fix it.
Understanding Hardware Error 3
Hardware Error 3 in mowers is a frequent problem caused by various factors. It is an indication that a specific hardware component or system in your lawn mower is malfunctioning. This error can manifest in different ways, such as an error code on the display panel or the mower abruptly shutting down during operation. If not addressed promptly, it can lead to further damage to the mower’s components and disrupt your lawn maintenance routine.
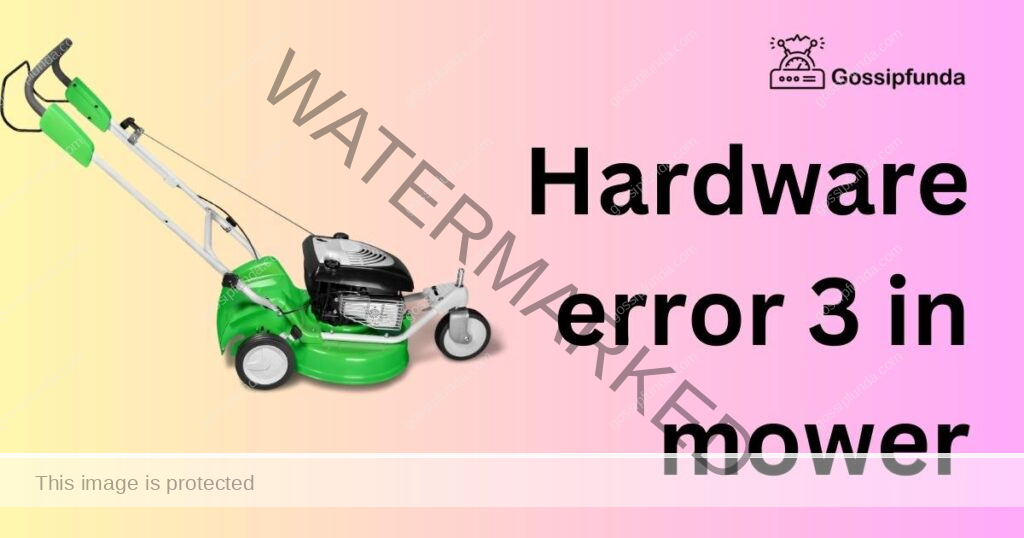
Common Causes of Hardware Error 3
- Sensor Malfunction: One of the primary reasons behind hardware error 3 is a malfunctioning sensor. Modern mowers utilize sensors to monitor various aspects, such as blade speed, oil levels, or temperature. A faulty sensor can send incorrect signals to the mower’s control unit, triggering the error.
- Electrical Wiring Issues: Damaged or loose electrical wiring can disrupt the flow of crucial data between different components, leading to a hardware error. Exposure to moisture, rodents, or wear and tear over time can all contribute to wiring problems.
- Overheating Components: Mowers work in challenging outdoor conditions, and their components can overheat due to prolonged use or inadequate cooling. This can trigger hardware error 3 as a protective measure to prevent damage.
- Faulty Control Board: The control board acts as the brain of the mower, interpreting signals and ensuring proper functioning. A defective control board can misinterpret data and lead to erroneous error messages.
- Battery Issues: Weak or damaged batteries can cause voltage fluctuations, resulting in hardware errors.
- Mechanical Failures: Hardware error 3 can also occur due to mechanical failures in critical components, such as the engine, blade assembly, or transmission system.
How to fix hardware error 3 in mower?
Fix 1: Check and Clean Sensors for Hardware Error 3
When facing hardware error 3 in your mower, one of the first steps to take is to inspect and clean the sensors. Sensors play a crucial role in monitoring various aspects of the mower’s operation, and a malfunctioning sensor can often be the culprit behind this error.
Step 1: Locate the Sensors
Refer to your mower’s user manual to identify the location of sensors. Common sensors include those for blade speed, oil levels, temperature, and safety features. They are usually situated near the critical components of the mower.
Step 2: Turn off the Mower
Before proceeding, ensure the mower is turned off and disconnected from any power source to avoid accidents.
Step 3: Inspect for Damage
Carefully examine each sensor for signs of physical damage or wear. Look for any cracks, breaks, or loose connections. If any sensor appears damaged, it may need to be replaced.
Step 4: Clean the Sensors
Dirt, grass clippings, and debris can accumulate around the sensors over time, affecting their performance. Use a soft cloth or brush to gently clean the sensors, ensuring they are free from any obstructions. Be cautious not to damage the delicate sensor components during cleaning.
Step 5: Check Sensor Connections
Ensure that all sensor connections are secure and properly attached. Loose connections can lead to inaccurate readings and trigger the hardware error.
Step 6: Test the Sensors
After cleaning and securing the connections, it’s essential to test the sensors. Some mowers have a diagnostic mode that allows you to check the sensors’ functionality. Consult your user manual for instructions on how to access the diagnostic mode.
Step 7: Replace Faulty Sensors (if necessary)
If you find any sensors that are damaged beyond repair or continue to malfunction despite cleaning, it’s time to replace them. Contact your mower’s manufacturer or an authorized dealer to get genuine replacement parts.
Step 8: Perform a Test Run
After cleaning and, if needed, replacing the sensors, restart the mower and perform a test run. Observe its performance and check if the hardware error 3 message persists. If the issue is resolved, you can resume regular mowing operations.
By checking and cleaning the sensors, you can address sensor-related issues causing hardware error 3. However, if the error persists, don’t worry; there are more troubleshooting steps to explore. Always prioritize safety and follow the manufacturer’s guidelines during maintenance and repairs.
Read more: Why are my notifications not showing up on iPhone
Fix 2: Inspect and Repair Electrical Wiring
When dealing with hardware error 3 in your mower, another potential culprit could be faulty or damaged electrical wiring. Wiring issues can disrupt the flow of crucial data between components, leading to error messages and malfunctions.
Step 1: Safety First
Before you start inspecting the electrical wiring, ensure the mower is turned off and disconnected from any power source. Additionally, wear appropriate safety gear to protect yourself from any electrical hazards.
Step 2: Visual Inspection
Carefully examine all electrical connections, wires, and harnesses for signs of wear, corrosion, or damage. Look for frayed wires, loose connections, or any exposed areas. Identifying the source of the issue will help you determine the necessary repairs.
Step 3: Tighten Loose Connections
If you find any loose connections, gently tighten them using the appropriate tools. Ensure the connections are snug but not overly tight, as excessive force can cause damage.
Step 4: Repair Damaged Wires
For wires with visible damage, such as cuts or breaks, you’ll need to repair or replace them. Use wire strippers to remove the damaged portion, and then use connectors or soldering (depending on the type of wire) to join the pieces back together securely.
Step 5: Protective Sleeves
To prevent future wiring issues, consider using protective sleeves or conduit to cover exposed wires. These sleeves can shield the wiring from environmental factors such as moisture, dust, and pests.
Step 6: Testing Continuity
If you suspect a wiring problem but cannot visually identify the issue, use a multimeter to test for continuity along the wires. This will help pinpoint any breaks in the electrical circuit.
Step 7: Inspect Safety Switches
Safety switches play a vital role in the mower’s operation. Check the wiring and connections of the safety switches to ensure they are functioning correctly. Malfunctioning safety switches can trigger hardware error 3 as a safety precaution.
Step 8: Seek Professional Assistance
If you are unsure about repairing electrical components or if the issue persists after performing these steps, it’s best to seek help from a qualified technician. They have the expertise to diagnose and address complex electrical problems safely.
Remember that electrical components can be sensitive, and improper handling may cause more harm than good. Always follow manufacturer guidelines and safety precautions when working with electrical systems.
By carefully inspecting and repairing electrical wiring, you can resolve hardware error 3 issues related to electrical malfunctions and enjoy uninterrupted mowing sessions once again.
Fix 3: Addressing Overheating Components
Hardware error 3 in your mower may also be triggered by components overheating during operation. Overheating can lead to the activation of safety mechanisms, causing the error message to appear and halting the mower’s function.
Step 1: Let the Mower Cool Down
If you encounter hardware error 3 while mowing, immediately turn off the mower and let it cool down. Avoid attempting any repairs while the engine is still hot to prevent the risk of burns.
Step 2: Check the Cooling System
Inspect the cooling system components, such as the cooling fan, radiator, and air vents, for any signs of obstruction or damage. Accumulated debris, grass clippings, and dirt can impede airflow, leading to overheating. Clean these components thoroughly using a soft brush or compressed air to remove any blockages.
Step 3: Inspect the Engine Oil
Low engine oil levels can contribute to overheating issues. Check the oil level using the dipstick (with the mower on a level surface) and add oil if necessary. Ensure you are using the type of oil recommended by the manufacturer.
Step 4: Check the Cooling Fan
The cooling fan plays a vital role in dissipating heat from the engine. Start the mower and observe the cooling fan during operation. If it does not spin or spins sluggishly, it may be faulty and require replacement.
Step 5: Monitor the Airflow
Ensure that the cooling vents and air passages are free from any obstruction. Adequate airflow is crucial for keeping the engine and other components at optimal temperatures.
Step 6: Operate the Mower Correctly
Avoid pushing your mower beyond its capacity by mowing excessively tall or thick grass in a single pass. Cutting the grass in stages and at a reasonable height will help prevent overheating.
Step 7: Maintain Air Filters
Dirty or clogged air filters can hinder proper airflow to the engine, contributing to overheating. Regularly clean or replace air filters according to the manufacturer’s guidelines.
Step 8: Test Run
After performing the above steps, restart the mower and perform a test run. Monitor the temperature gauge or indicator, if available, to ensure that the components are operating within the recommended temperature range.
Step 9: Professional Assessment
If the hardware error 3 persists despite your efforts, it may be due to more complex issues that require professional attention. Seek the assistance of a certified technician to diagnose and address any underlying problems.
By addressing overheating issues, you can prevent hardware error 3 and extend the life of your mower’s components. Regular maintenance and proper operation will help keep your mower running smoothly, ensuring your lawn remains in pristine condition.
Fix 4: Assessing the Control Board
If hardware error 3 continues to trouble your mower after examining sensors, electrical wiring, and overheating issues, it’s essential to focus on the control board. The control board serves as the central processing unit of the mower, interpreting data and ensuring the correct functioning of various components.
Step 1: Safety Precautions
Before working on the control board, turn off the mower, disconnect it from any power source, and wear appropriate safety gear to avoid electrical hazards.
Step 2: Locate the Control Board
Refer to the user manual to identify the control board’s location in your mower. Usually, it is housed within the mower’s control panel or engine compartment.
Step 3: Visual Inspection
Carefully examine the control board for any visible signs of damage, such as burnt spots, melted components, or loose connections. A damaged control board may require replacement.
Step 4: Check for Loose Connections
Gently check all the connections on the control board for tightness. Loose connections can lead to improper data transmission and trigger hardware error 3. Ensure all connectors are securely plugged in.
Step 5: Power Cycle the Mower
Sometimes, errors can be resolved by power cycling the mower. Turn off the mower, disconnect the battery or power source, wait for a few minutes, and then reconnect the power. Restart the mower to see if the error clears.
Step 6: Reset the Control Board
If the control board has a reset button or function, you can try resetting it to its default settings. Refer to the user manual for instructions on how to perform a reset properly.
Step 7: Professional Inspection
If you are uncertain about handling the control board or if the error persists despite your efforts, it’s best to seek professional assistance. Certified technicians have the expertise and equipment to diagnose control board issues accurately.
Step 8: Consider Control Board Replacement
If the control board appears severely damaged or has undergone extensive wear and tear, replacing it might be the most effective solution. Contact your mower’s manufacturer or an authorized dealer to obtain a compatible control board.
Step 9: Final Test
After performing any repairs or replacements, conduct a final test run to check if hardware error 3 has been resolved. Monitor the mower’s performance to ensure smooth operation.
Hardware error 3 in your mower can be caused by various factors, and it may require a systematic approach to identify and resolve the issue. By inspecting and addressing potential causes such as sensors, electrical wiring, overheating, and the control board, you can overcome this problem and enjoy hassle-free mowing sessions. Remember to follow safety guidelines, consult the user manual, and seek professional help when necessary to keep your mower in top-notch condition and your lawn looking pristine.
Fix 5: Checking and Replacing the Battery
A weak or damaged battery can lead to voltage fluctuations, triggering hardware error 3 in your mower. Ensuring that the battery is in good condition is crucial for the proper functioning of the mower’s electrical system.
Step 1: Safety Precautions
Before working on the battery, turn off the mower and disconnect it from any power source. Wear appropriate safety gear to protect yourself from any accidental spills or electrical hazards.
Step 2: Locate the Battery
Refer to the mower’s user manual to find the battery’s location. In most mowers, the battery can be found near the engine or beneath the seat.
Step 3: Inspect the Battery
Carefully examine the battery for any visible signs of damage, leakage, or corrosion. Corrosion on the terminals can hinder proper electrical connections.
Step 4: Check the Battery Voltage
Using a multimeter, measure the battery’s voltage. A fully charged battery should read close to the manufacturer’s recommended voltage. If the voltage is significantly lower, the battery may need to be charged or replaced.
Step 5: Charge the Battery
If the battery voltage is low, charge it using an appropriate battery charger according to the manufacturer’s instructions. Ensure the charger is compatible with your battery type.
Step 6: Clean the Battery Terminals
If you notice any corrosion on the battery terminals, clean them using a mixture of baking soda and water. Gently scrub the terminals with a wire brush until they are clean. Rinse the terminals with water and dry them thoroughly.
Step 7: Reconnect the Battery
Once the battery is fully charged and the terminals are clean, reconnect the battery to the mower. Ensure the connections are tight and secure.
Step 8: Test Run
Start the mower and perform a test run to check if the hardware error 3 persists. Monitor the mower’s performance and check if the error message reappears.
Step 9: Battery Replacement (if necessary)
If the battery is old, damaged, or unable to hold a charge, it may need to be replaced. Purchase a new battery that matches the specifications recommended by the manufacturer.
Step 10: Dispose of Old Battery Properly
If you replace the battery, dispose of the old battery following local regulations and guidelines for battery recycling.
Fix 6: Addressing Mechanical Failures
If you have tried the previous fixes and hardware error 3 still persists, it is essential to investigate potential mechanical failures within your mower. Mechanical issues in critical components can trigger this error and disrupt your lawn mowing routine.
Step 1: Safety Precautions
Before examining any mechanical components, turn off the mower and disconnect it from any power source. Wear appropriate safety gear, such as gloves and eye protection, to prevent injuries.
Step 2: Inspect the Blade Assembly
Carefully examine the blade assembly for any visible damage, such as bent or dull blades. Bent blades can cause imbalances, leading to hardware errors during operation. If the blades are damaged, replace them with sharp and correctly aligned ones.
Step 3: Check the Transmission System
Inspect the transmission system, including belts and pulleys, for signs of wear or misalignment. A faulty transmission system can cause hardware error 3 or other operational issues. Adjust or replace any damaged components as needed.
Step 4: Examine the Engine
The engine is the heart of your mower, and any mechanical issues can lead to hardware errors. Check for oil leaks, unusual noises, or performance issues. Consult a professional mechanic or the mower’s manufacturer if you suspect engine problems.
Step 5: Test the Mower’s Performance
Start the mower and perform a test run. Observe its performance closely, paying attention to any unusual vibrations, sounds, or unexpected shutdowns. Address any mechanical abnormalities promptly.
Step 6: Lubrication
Ensure that all moving parts, such as wheel axles and linkages, are properly lubricated. Lubrication reduces friction, which can prevent mechanical failures and improve overall mower performance.
Step 7: Regular Maintenance
Implement a regular maintenance schedule for your mower, including blade sharpening, oil changes, and cleaning. Preventive maintenance can help identify and address potential mechanical issues before they escalate.
Step 8: Seek Professional Help
If you are unable to identify or resolve the mechanical problem on your own, consider seeking assistance from a certified technician or a reputable mower repair service. They can diagnose the issue accurately and provide appropriate solutions.
Fix 7: Performing Regular Maintenance
While we have explored specific fixes for hardware error 3, it’s essential not to overlook the significance of regular maintenance in preventing and addressing such errors. A well-maintained mower is less likely to encounter hardware issues, ensuring a seamless mowing experience.
Step 1: Refer to the User Manual
Familiarize yourself with the user manual provided by the mower’s manufacturer. The manual contains valuable information on maintenance schedules, recommended procedures, and troubleshooting guides.
Step 2: Cleaning the Mower
After each use, clean the mower thoroughly to remove grass clippings, dirt, and debris. Pay particular attention to the underside of the deck and the cooling vents to maintain proper airflow.
Step 3: Inspect Belts and Pulleys
Regularly inspect the belts and pulleys in the transmission system for signs of wear, cracking, or misalignment. Replace any damaged components promptly.
Step 4: Sharpen the Blades
Dull blades can strain the mower’s engine and trigger errors. Sharpen the blades regularly to ensure a clean and efficient cut.
Step 5: Check the Oil and Fuel
Monitor the oil and fuel levels before each use. Top up or replace them as needed, following the manufacturer’s recommendations.
Step 6: Lubricate Moving Parts
Apply lubricant to moving parts, such as wheel axles, bearings, and pivot points, to reduce friction and prolong their lifespan.
Step 7: Inspect Air Filters
Clean or replace air filters according to the recommended schedule to maintain proper airflow to the engine.
Step 8: Inspect and Tighten Fasteners
Regularly check and tighten all nuts, bolts, and fasteners to ensure that the mower’s components are securely in place.
Step 9: Store the Mower Properly
When not in use, store the mower in a dry and covered area. Avoid leaving it exposed to harsh weather conditions that can accelerate wear and tear.
Step 10: Keep a Maintenance Log
Maintain a maintenance log to track the tasks performed and the dates when they were completed. This helps you stay organized and ensures that you don’t miss any essential maintenance tasks.
Fix 8: Software Updates and Firmware Checks
In some cases, hardware error 3 in your mower could be caused by outdated or corrupted software/firmware. Regularly checking for updates and ensuring that the mower’s software is up-to-date can help prevent such errors.
Step 1: Check for Manufacturer Updates
Visit the manufacturer’s website or contact their customer support to inquire about any available software updates for your mower model. Manufacturers often release updates to address bugs, improve performance, and enhance safety features.
Step 2: Download and Install Updates
If updates are available, download them following the manufacturer’s instructions. Install the updates on your mower as directed to ensure that it has the latest software version.
Step 3: Reset the Firmware
Some mowers have firmware that controls various functions. If your mower has firmware, consider resetting it to its default settings after installing updates. Refer to the user manual for instructions on how to perform a firmware reset correctly.
Step 4: Backup Settings
If your mower has customizable settings, consider backing them up before performing any software updates or firmware resets. This way, you can easily restore your preferred settings after the update.
Step 5: Test Run
After installing updates or resetting firmware, start the mower and perform a test run. Observe its performance to check if the hardware error 3 persists. Properly updated software/firmware can resolve many software-related issues.
Step 6: Address Firmware Corruption
If you suspect that the firmware might be corrupted, contact the manufacturer for guidance on how to restore or reinstall the firmware properly.
Step 7: Maintenance of Electronic Components
Keep electronic components, such as control panels and displays, clean and free from moisture to prevent software glitches caused by water damage.
Step 8: Stay Informed
Stay informed about any recalls or software-related issues specific to your mower model. Manufacturers may issue recalls or provide solutions for known software problems.
Step 9: Follow Guidelines
Always follow the manufacturer’s guidelines when updating software or firmware to avoid any potential complications.
Preventing Hardware Error 3: Maintenance Tips for a Smooth Mowing Experience
Mowing your lawn can be a breeze when you take preventive measures to avoid hardware error 3. Here are some essential tips to maintain your mower and ensure it operates smoothly:
1. Regular Maintenance is Key
Implement a consistent maintenance schedule that includes cleaning, blade sharpening, oil changes, and air filter checks. Preventive maintenance can catch potential issues before they escalate into hardware errors.
2. Keep the Mower Clean
Clean your mower after each use to remove grass clippings, dirt, and debris. Pay special attention to the cooling vents and underside of the deck to maintain proper airflow and prevent overheating.
3. Inspect and Replace Blades
Dull or damaged blades strain the mower’s engine and can trigger errors. Regularly inspect and sharpen or replace blades as needed to ensure a clean and efficient cut.
4. Check Electrical Connections
Regularly inspect the electrical connections for tightness and signs of wear. Loose connections can cause voltage fluctuations and lead to hardware errors.
5. Maintain Proper Tire Pressure
Ensure that your mower’s tires are inflated to the recommended pressure. Proper tire pressure improves maneuverability and prevents excessive strain on the mower’s components.
6. Store the Mower Correctly
When not in use, store the mower in a dry and covered area. Avoid exposing it to harsh weather conditions that can accelerate wear and tear.
7. Use High-Quality Fuel and Oil
Use high-quality fuel and oil recommended by the manufacturer. Poor-quality fuel can cause engine problems, leading to hardware errors.
8. Address Issues Promptly
If you notice any unusual noises, vibrations, or performance issues while mowing, address them promptly. Ignoring problems can worsen the situation and lead to hardware errors.
9. Follow User Manual Guidelines
Refer to the user manual for specific maintenance guidelines and troubleshooting tips. Following the manufacturer’s recommendations ensures you take the best care of your mower.
10. Professional Maintenance
Consider scheduling periodic professional maintenance for your mower. Certified technicians can conduct thorough inspections and address potential issues that you may have missed.
By following these preventive tips and maintaining your mower regularly, you can minimize the risk of encountering hardware error 3 and enjoy a seamless mowing experience throughout the season. A well-maintained mower not only operates efficiently but also extends its lifespan, saving you from costly repairs in the long run.
Conclusion
Hardware error 3 in your mower can be an annoying roadblock in your lawn maintenance routine. By understanding the common causes behind this error and following our step-by-step troubleshooting guide, you can get your mower back in pristine condition. Regular maintenance, proper storage, and handling can also prevent such errors in the future. Remember, safety is paramount, and if you’re unsure about any repair process, it’s best to seek professional help. Happy mowing!
FAQs
It’s a common issue indicating malfunction in critical mower components.
It can be due to sensor issues, wiring problems, or overheating components.
Check sensors, clean wiring, address overheating, and update software/firmware.
Yes, you can follow troubleshooting steps, but seek professional help if needed.
Regular maintenance, cleaning, and using high-quality fuel are preventive measures.
Contact a certified technician for a comprehensive diagnosis and proper resolution.
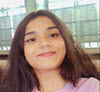
Prachi Mishra is a talented Digital Marketer and Technical Content Writer with a passion for creating impactful content and optimizing it for online platforms. With a strong background in marketing and a deep understanding of SEO and digital marketing strategies, Prachi has helped several businesses increase their online visibility and drive more traffic to their websites.
As a technical content writer, Prachi has extensive experience in creating engaging and informative content for a range of industries, including technology, finance, healthcare, and more. Her ability to simplify complex concepts and present them in a clear and concise manner has made her a valuable asset to her clients.
Prachi is a self-motivated and goal-oriented professional who is committed to delivering high-quality work that exceeds her clients’ expectations. She has a keen eye for detail and is always willing to go the extra mile to ensure that her work is accurate, informative, and engaging.